The Do's and Don’ts of Decorative Overlayments
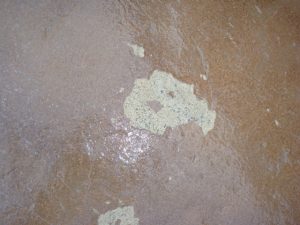
With a dizzying number of cementitous decorative resurfacing and overlayment products on market, contractors and application specialists can run into many problems. Often, the most common problems have solutions that are relatively easy if an individual takes time to understand why the problem occurred in the first place and how the simple fix works.
Test concrete substrates to avoid coating failures. Testing all concrete for pH, moisture and surface porosity are essential to ensure co-adhesion to the substrate. The best way to test surface porosity is to puddle water on the surface. The water should penetrate immediately. If not, the surface needs to be profiled until the water does penetrate. If the surface isn’t porous, the coating won’t penetrate. Additionally, the pH level should not be higher than 12 and can be checked using a pH pencil and distilled water. Theconcrete moisture vapor transmissions can be tested using the Calcium Chloride Test kit in compliance with ASTM- F2170. The concrete should have no more than (3 lbs.) of pressure coming through the concrete per (1,000 sq. ft).
Crack reflection through repaired cracks. Although crack reflection through the overlay should never be warranted by the application contractor since concrete expands and contracts with earth movement and weather conditions, the applicator can saw-cut the existing expansion joints (full depth) and add additional full-depth expansion joints to relieve the stress on the cracks.
Coating failures adjacent to expansion joints. Failures near the expansion joints are normally caused by excess materials from the joints, which should have been removed. All cementitious materials should always be removed from the joints, and expansion joints should benefit from caulking. Rope or taping off the joints can avoid material from entering the joints. If the joints are being filled because they have deteriorated, then repaired expansion joints should be re-cut to original width and depth.
Hot tire pickup and staining from vehicle traffic. Delamination of stains and sealers in vehicular traffic areas – or “hot tire pick up” – is caused by improper sealer selection. Be sure to select a sealer that is designed for vehicular traffic areas. Failure to select the proper sealer can also lead to permeant staining or tire marks.
Fisheyes or surfaces repelling stains and sealers on stamped overlays. It is essential that for both new stamped concrete, as well as overlays, all liquid release agents and accompanying residue are removed using a mild (non-lotion) detergent prior to applying stains or protective sealers. Liquid releases are comprised oils that will repel the stains and sealers.
Using compatible products. It is very important to use a single manufacturer’s product line or systems to ensure proper adhesion and compatibility. For example, some sealers are designed to penetrate porous surfaces, while others are designed to be applied over sealed or stained surfaces. Using the wrong product can make a big difference in overall project quality.
Testing for coating, stain and sealer adhesion. Prior to applying coatings, stains or sealers, it is always recommended to do a test patch. After curing of the sample, attach duct tape to the surface and allow it to bond for about an hour. Rip off the duct tape and see if adjustments need to be made.